Hi all,
I open this thread, to share my project, and have the maximum amount of advice from the community.
I will equip the bucket seat and the pedals;
But for now, I'm going to focus on the bucket seat.
The bass shaker used will be:
Behind the seat: 8 x Dayton DAEX32EP-4 (stereo)
Under the seat: 2x Buttkicker Concert (Large) (Mono)
seat side: Buttkicker LFE (Large) (Stereo)
And why not TST 329 Gold (Stereo).
Sound card: Focusrite Scarlett 18i20 (Apparently you can only use the equalizer for instrument outputs) I have to go to the specialist store for advice, as I have seen this reference from other TASCAM US- 16X08.
The amps will be Behringer DSP for BK and TST, for Dayton it will be 4 Behringer channels.
The most important thing for me right now is to have excellent vibration conduction in the bucket seat.
To cut the vibrations, I chose this: RSM406-45
[URL unfurl = "true"] https://www.avindustrialproducts.co.uk/files/ww/47. Rectangular Sandwich Mountings.pdf [/ URL]
Thank you [USER = 242956] @Mr Latte [/ USER] for the link
They will be placed below, in the red zone (see photo).
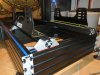
I drew on Solidworks 2 plates that would support the BK. It is a first solution.
yellow legend: Central plate, will be fixed on the lateral supports.
Blue Legend: side plate for BK-LFE, which will be fixed under the bucket seat support and placed outside.
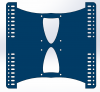
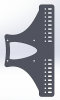
I still don't know how to put the TST329G
All suggestions are obviously welcome.
Dadz
I open this thread, to share my project, and have the maximum amount of advice from the community.
I will equip the bucket seat and the pedals;
But for now, I'm going to focus on the bucket seat.
The bass shaker used will be:
Behind the seat: 8 x Dayton DAEX32EP-4 (stereo)
Under the seat: 2x Buttkicker Concert (Large) (Mono)
seat side: Buttkicker LFE (Large) (Stereo)
And why not TST 329 Gold (Stereo).
Sound card: Focusrite Scarlett 18i20 (Apparently you can only use the equalizer for instrument outputs) I have to go to the specialist store for advice, as I have seen this reference from other TASCAM US- 16X08.
The amps will be Behringer DSP for BK and TST, for Dayton it will be 4 Behringer channels.
The most important thing for me right now is to have excellent vibration conduction in the bucket seat.
To cut the vibrations, I chose this: RSM406-45
[URL unfurl = "true"] https://www.avindustrialproducts.co.uk/files/ww/47. Rectangular Sandwich Mountings.pdf [/ URL]
Thank you [USER = 242956] @Mr Latte [/ USER] for the link
They will be placed below, in the red zone (see photo).
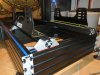
I drew on Solidworks 2 plates that would support the BK. It is a first solution.
yellow legend: Central plate, will be fixed on the lateral supports.
Blue Legend: side plate for BK-LFE, which will be fixed under the bucket seat support and placed outside.
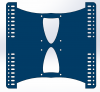
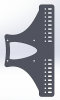
I still don't know how to put the TST329G
All suggestions are obviously welcome.
Dadz
Last edited: